5 Most Important Steps of Shipping Container Construction
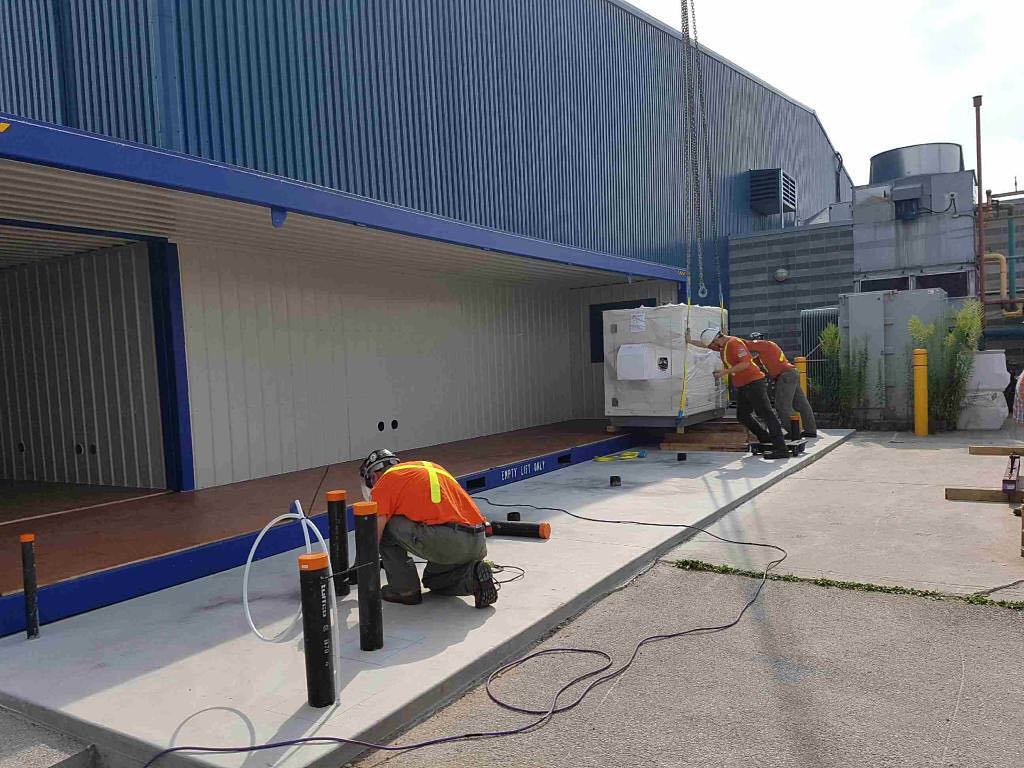
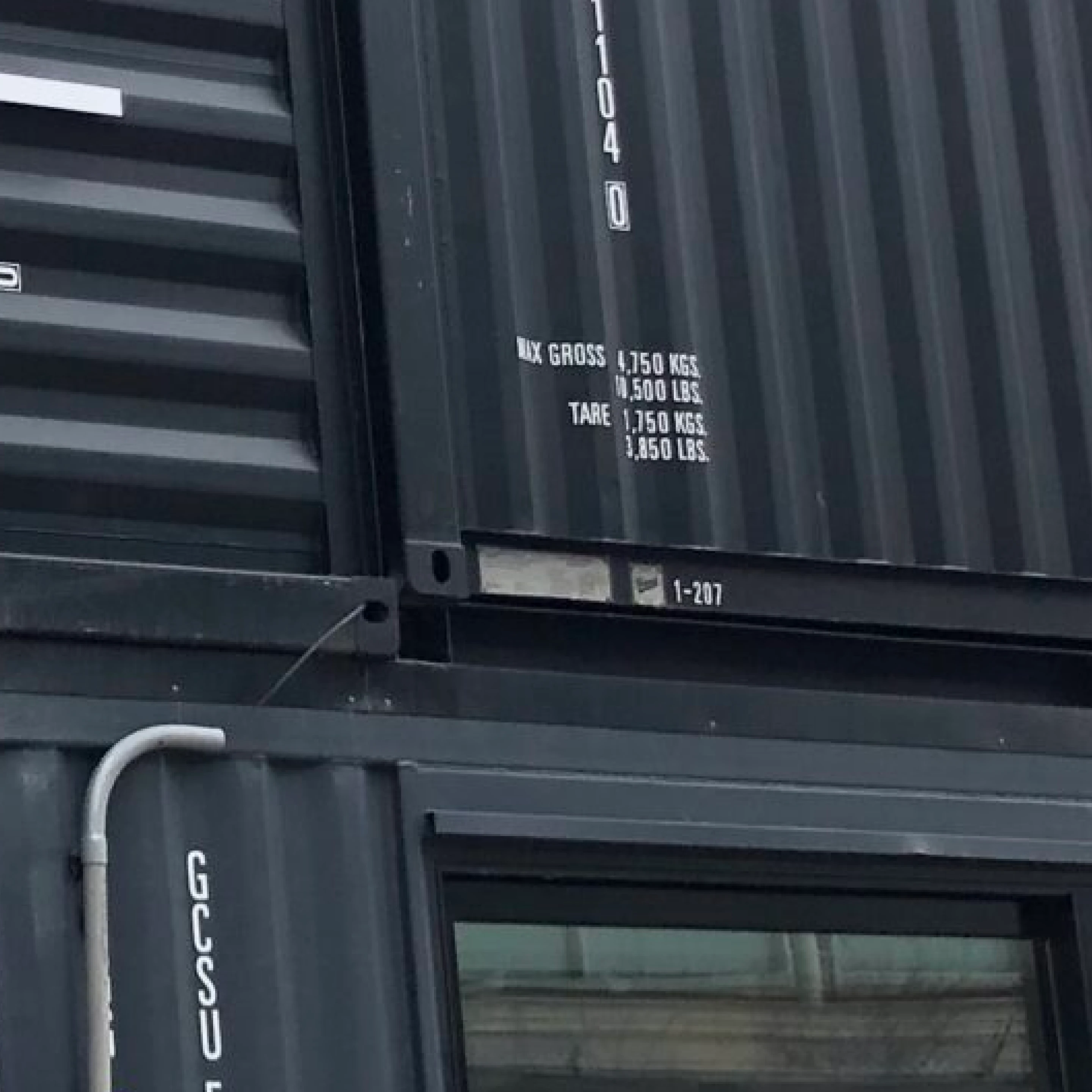
1. Installing Insulation
This is one of the most crucial steps of the build due to fluctuation of temperatures - although the steel walls may protect you against the outside forces, they do not hold the ability to maintain comfortable temperatures. Similarly to classic home builds, they need insulation.
Properly insulating the container prior to construction will ensure comfortable maintenance of temperatures all year around. It will also be much more efficient energy wise which will be lighter on your wallet.
Without insulation your build will loose heat easier and find excessive moisture inside the home - this of course turning into mold.
Regardless of the type of insulation you decide to install, you need to make sure it is installed correctly. There are two different ways:
- With spray foam insulation: ensuring a vapor barrier is created.
- Panel insulation: fitting them with the foil the correct way around.
A lot of people don't take into account the bottom of the container holds the same risks, so make sure all four sides of the container are properly insulated.
Lastly, different climates are also important to take into consideration when choosing which type of insulation you're using - if you live in a cold climate you will want to look at using spray foam insulation. Whereas in a dry, mild climate you could use panel insulation.
2. Zoning Permits
This particular stage has the potential to completely call off the build before it even starts!
Some regional planning departments are still yet to warm up to the idea of shipping container architecture. As you might expect, getting a permit in areas familiar with shipping container homes is far easier than those areas with no previous builds.
Prior to purchasing any land, approach your local planning department to make sure they are comfortable with the idea of a shipping container build. Doing this will save you a lot of time and headache, unlike Robert Fidler who build his home without a permit at a cost of $1.5 million and was forced to pull the building down.
3. Planning Your Build
“A failure to plan is a plan to fail.”
Like every other build plans, it's important and a huge time saver to catch mistakes and potential wrong-doings on paper before it hits the production stage.
When planning your build, some of the key things to think about are: budget, design, zoning, and project timeline.
4. Setting a Realistic Budget
As previously mentioned following a solid plan is incredibly important, but assigning a specific budget that properly meets this plan is easily just as important. Not a lot of people realize just how many expenses come along with building a container home.
A couple things to keep in mind when putting your budget together:
- Permits
- The containers themselves: we encourage repurpose of shipping containers rather than using new ones, it's easier on your wallet and eco-friendly.
- Insulation
- Window instalment
- Additional build pieces
- Roofing and flooring
- Painting and finishes
We recommend that you have a contingency allowance of 20% - even with the best plan, unexpected things can and will occur during your build. Remember...“Hope for the best, but plan for the worst" and "Better to have it and not need it, then need it and not have it.”
5. Rust Treatment and Prevention
Regardless of the material you choose to build your house with, tradeoffs and weaknesses are a fact of life. Wooden homes are exposed to decay and termite infestation. Concrete homes are faced with cracking, settling, and crumbling. With shipping container homes, the primary issues are rust and corrosion.
Shipping containers are built out of Corten steel and coated with anti-corrosive paint when new. Throughout the construction period when you are cutting and modifying your container some of the protective paint is most likely to chip and get stripped away. During the construction, when you are cutting and modifying the containers, you will likely strip away some of the protective paint. This can leave your shipping containers exposed to the elements. This is why it’s crucial you treat your shipping containers for corrosion during the build and cover any bare metal.
Even after you’ve finished your build and moved in, you still need to keep an eye out for rust and corrosion.
Need some more inspiration?
Check out our recent projects
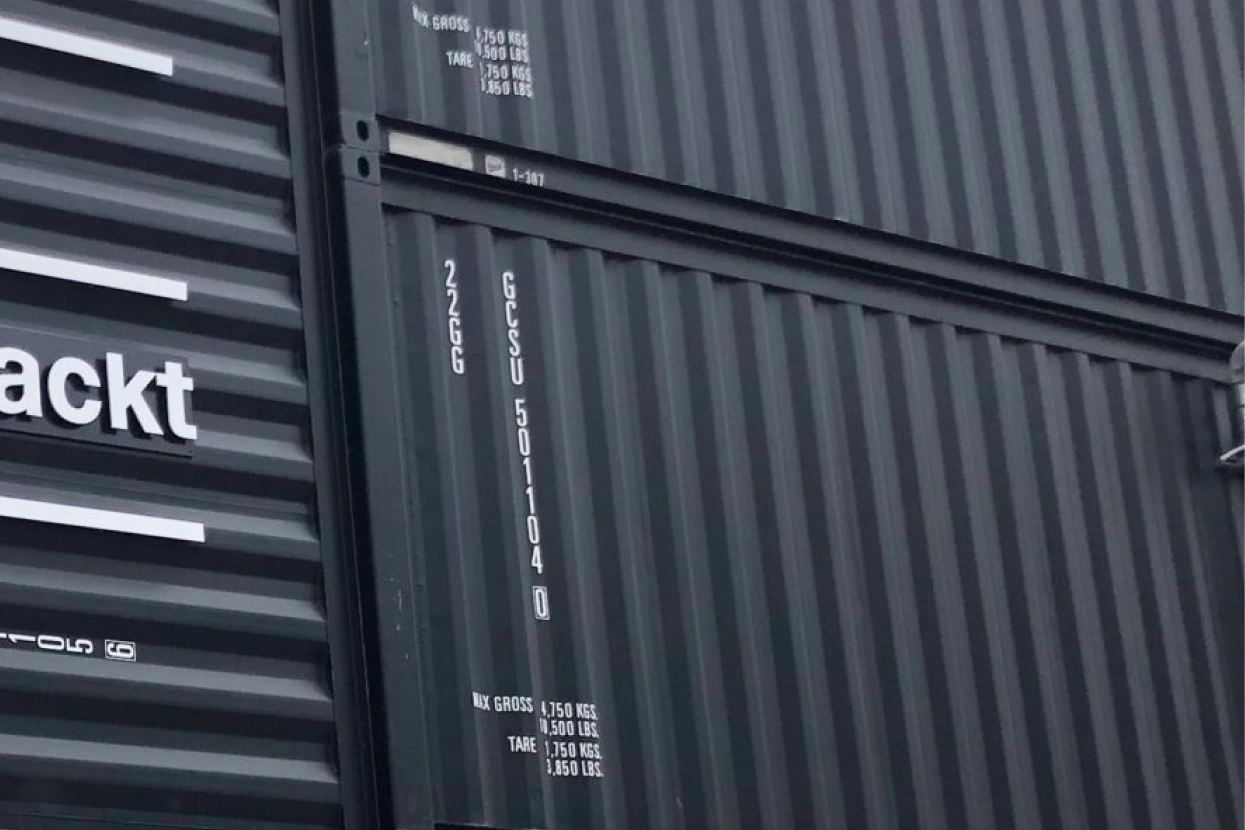